- Epoxy Primers
- Epoxy Paints
- Polyurethane Primer
- Polyurethane Paints
- Enamel Primers
- Enamel Paint
- Alkaline Degreaser
- Universal Cleaner
- Aluminium Chromating
- Etch Primer
- Rust Converter
- Hot / Cold Phosphating
- De-ruster
- De-watering oil
- High Temperature Silicone Paints
- Chlorinated Rubber Paint
- Acrylic Vinyl Paint
- Zinc Silicate Coating
- Water Based Anti-Corrosive Paint
Contact us
For Business Opportunities, Product Purchases and Application Services
Anti Corrosive Coatings and Paints
Hot / Cold Phosphating
Phosphate coating is used for corrosion resistance and lubrication and as a foundation for subsequent coating or painting. It serves as a conversion coating in which a dilute solution of phosphoric acid and phosphate salt is applied via spraying or immersion and chemically reacts with the surface of the part being coated to form a layer of insoluble, crystalline phosphate. The process of phosphate coating is employed for the purpose of pretreatment prior to coating or painting, increasing corrosion protection. Most phosphate coatings serve as a surface preparation for further coating and/or painting, a function they perform effectively, with excellent adhesion and electric isolation. Zinc phosphate coatings are frequently used in conjunction with sodium stearate (soap) to form a lubrication layer in cold and hot forging. Cold phosphating has no advantage over hot phosphating apart from saving your heating costs.
However, cold phosphating requires more processing time to achieve the desired amount of phosphate coating weight. Iron phosphates are typically used as a base for further coating or painting and is applied by immersion or by spraying.
Zinc phosphates are used for corrosion resistance (phosphate and oil), a lubricant base layer, and as a paint/coating base and can also be applied by immersion or spraying.
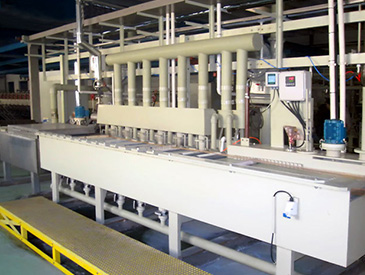
Our Application Services

Advanced Technology

Application Experts

Commitment to Quality
Request a Quote
Please use the form below to send us your projects and comments. We appreciate you taking the time to provide us with your views so that we can best meet the needs of you. We aim to provide a seamless experience to all our users.
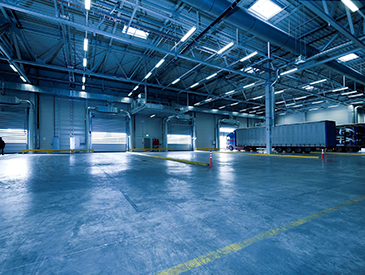
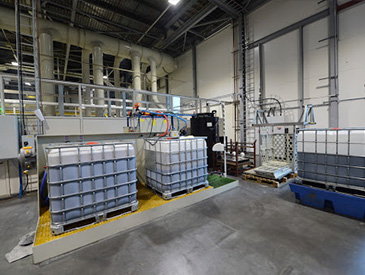
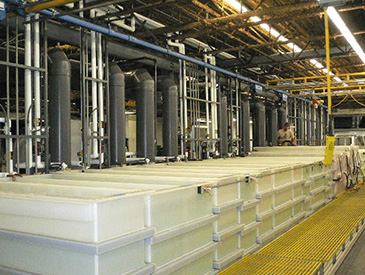